What are the Roles in Six Sigma?
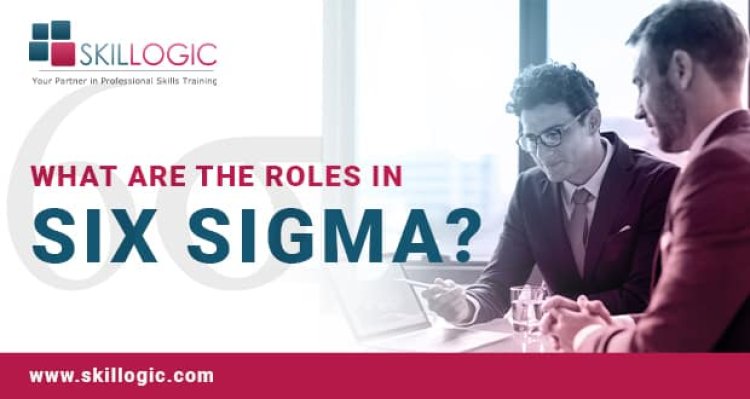
Six Sigma was developed for the first time in 1987 by William Bill Smith who worked as an engineer at Motorola. Today, “Six Sigma” is not just a term related to statistics but a catchphrase in the business world as an efficient quality management tool. The technique emphasizes the significance of customer satisfaction and the growth of a company.
Six Sigma essentially connotes a quality measure taken by organizations or businesses that aims for high-grade functioning. The word could be replaced as “Operational Excellence,” “Zero Defects,” or “Customer Perfection” according to different company needs and requirements.
Watch this video: What is Six Sigma
Perks of Using Six Sigma
- The principal purpose of Six Sigma is to attain customer satisfaction and to secure the objective, copious methods are pursued to refine the performance of a product or business process.
- The methodology helps curtail shortcomings, elevate profits, and enhances both staff morale and product quality.
- Six Sigma is used to pinpoint and minimize errors and the productivity of business processes.
- Using Six Sigma methodology, you can make precise and legitimate business decisions based on available data.
- Six Sigma centers around facts and these facts can help you maximize your success for the future.
You can refer this article for “What Is The Cost Of Six Sigma Certifications In India?”
Roles In Six Sigma:
1. Executive
Executives constitute the most senior degree of leadership within the Six Sigma hierarchy. Executives are the highest trained in this area with greater experience level. Executives are competent with the leadership skills to strategize and to focus the Six Sigma program in accordance with an organization’s specific culture and goals. By overseeing the Six Sigma process and issuing support regarding methods and organization, Executives make certain that projects add value and success
2. Six Sigma Champions
Six Sigma Champion bears a key role at a senior or middle executive level. Sigma champions are usually upper-level managers who manage and distribute resources to upgrade process improvements and black belt development. Champions are upskilled in the central concepts of six sigma and the deployment tactics used by their organization.
- It is the duty of the Champion to comprehend the vision, mission, and metrics of the company and utilize this information to tune the Six Sigma plan to fit the corporation’s goals.
- They point out and get rid of roadblocks that could hinder process success. Six Sigma champions guide the implementation of the six sigma program.
- Execute and support the introduction of Six Sigma within the firm.
- Company executives who stand at the forefront of Six Sigma by backing projects.
- Leaders who are accountable for selecting employees to be “Belts” and coaching project leaders.
3. Six Sigma Master Black Belts:
Black belts masters are masters of the six sigma methodologies and are predominantly in full-time process improvement positions. They function as teachers who guide black belts and review their projects. The master black belts are chosen following up their ability to teach and mentor and also by evaluating their quantitative skills.
- They have a progressive understanding of the Statistical Tools used within Six Sigma.
- They coordinate with a Champion to proffer support and provide Project Descriptions.
- They are experts in directing and guiding Green Belts and Black Belts.
- They have comprehensive project management knowledge.
- They are the potential leaders of a corporation.
4. Six Sigma Black Belts
The term black belt is taken from martial arts. In Martial arts, the black belt is the expert who instructs and tutors others and exhibits a mastery of the art. Six Sigma black belts are most productive in full-time process development positions. Furthermore, six sigma black belts are those who have explored and showcased skill in the execution of the principles, practices, and techniques of six sigma for lower cost and higher profit.
- As a mentor, they will have a network of six sigma individuals in the company.
- As a teacher, they tutor local personnel.
- As a coach, they give support to personnel on local projects
- As an identifier, they engage in locating chances for improvement.
- They would be a champion of six sigma tools and strategy.
5. Green Belts
Six Sigma Green Belts are only occasionally occupied in full-time process improvement positions. Just as the black belt, the term green belt is also inspired by martial arts. The term denotes an individual who has acquired the basic skills but has limited experience when compared to black belts
- Green belts must exemplify expertise in statistical tools by employing them to make a positive financial impact and grant customer benefits.
- Individuals may remain green belts or they can become black belts with training on the same.
- Green belts work under the observation and direction of a black belt or master black belt.
6. Yellow Belts
Yellow Belts should have ample understanding of the basic metrics and improvement methods of Six Sigma as well as the skills to incorporate these tactics into an organization’s production systems. They personate the part of the principal team member in the six sigma process. Time and again, their proficiency in an area of knowledge can model them to be subject matter experts, with the commitment of managing smaller improvement projects. Yellow Belt Utilizes the Plan-Do-Check-Act methodology (PDCA) and is in charge of determining certain processes that need advancements. Being an introductory position within Six Sigma it is often asked to assist Green and Black Belts with projects.
7. White Belt
At the tyro level of Six Sigma, the White Belts will have a foundational introduction to the principles and methodologies of the program. They can function locally to resolve issues and assist projects. The individuals who have White Belt certification are often not members of the Six Sigma team. The White Belt level imparts a basic knowledge for the career ahead in six sigma.
Check Reviews for SKILLOGIC Six Sigma Certification Course.
Conclusion:
Businesses employ the Six Sigma methodology to enhance processes by discovering the errors that point to defects and implementing the latest management systems once the errors have been taken care of. Wish to pursue a career in Six Sigma? SKILLOGIC provides all-inclusive training in Six Sigma that is accredited by ICFQ and TUV. Join our training right now!
0
12505