The advantages of Lean Six Sigma
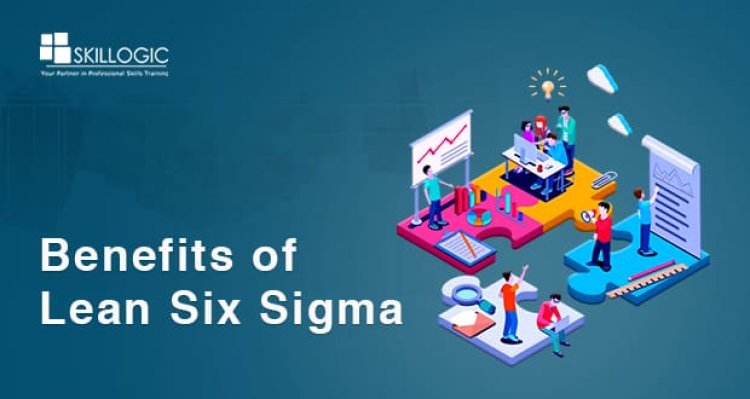
Lean Six Sigma is the perfect combination of two helpful techniques. With Six Sigma, a corporation may discover exactly how many problems, errors, flaws, inaccuracies, and other issues are occurring and then provide a systematic process to address them.
Lean focuses on lowering costs by eliminating many types of waste:
- Defects – Defects are poor quality differences in a product (broken pieces, faulty software, etc.). Bad quality control, inadequate standards, poor design, and inefficient operations are only a few of the reasons for faults.
- Overproduction – Occurs when a company produces more things than are required by customers. The products are simply a waste of money if they go unused.
- Waiting – Waiting happens when work must be halted owing to an external issue, such as a broken part, an overworked employee, or a lack of staffing. Employees are unable to create value during this time, resulting in inefficiency.
- Underutilized Talent – Wasteful administrative chores, poor communication, a lack of teamwork, and insufficient training are all examples of underutilised talent. Any company should strive to extract as much value as possible from its people.
- Transportation – Excessive transportation raises costs, wastes time, and raises the risk of product damage.
- Excess Inventory – This sort of waste arises when the supply of goods exceeds the demand of customers. Poor monitoring mechanisms and a lack of awareness of the customer’s needs are to blame.
- Motion Waste – Any unnecessary movement that does not add value to the product or service is referred to as motion waste. It can be caused by a lack of standards and a poorly designed procedure.
- When there are many copies of the same task or process, this is known as extra-processing.
Watch this video: What is Six Sigma?
How does Lean Six Sigma work for businesses?
- Customers will appreciate the value of products and services
Customer satisfaction, often known as customer loyalty, is one of the most important criteria in determining your company’s success. Only when your customers are completely satisfied with your products or services will they remain loyal to you. Lean Six Sigma improves service, delivery, and quality, all of which add value to customers and bring more business to the organisation.
- Increased productivity
Six Sigma can help you break down barriers and discover fundamental reasons for low productivity by allowing you to precisely evaluate time spent on activities. Six Sigma will assist you in addressing the underlying problem rather than beating about the bush blindfolded by collecting business-critical data from many areas.
- Strategic positioning that is more fluid
In terms of shifting conditions, Lean Six Sigma operations are more fluid and adaptable, allowing them to respond more quickly to unanticipated changes in the business or economic situation.
- A more competitive posture
Customers, sellers, and partners are attracted to the type of excellence and performance that Lean Six Sigma operations demonstrate, making these businesses more competitive in all aspects of operations.
- The achievement driven by the standards
Personnel training, project management and monitoring, problem-solving, and other elements of company operations are simplified and streamlined when processes are standardised.
- Improved innovation
When employees and management aren’t continuously fixing problems and overcoming obstacles, more innovative and imaginative thinking can flourish.
- Project lifecycle time is shorter
With Six Sigma methodology in place, you can form an exclusive team comprised of skilled individuals from various departments and levels within the firm. This group will then be tasked with identifying significant issues that could negatively affect the project and cause it to run late.
You lose money when you have a low-cost operation with faulty processes. One of the most effective strategies to cut costs is to gain a thorough grasp of an organization’s operations with the goal of improving them. The main goal of the Six Sigma technique, which comprises DMAIC, is to improve processes (Define, Measure, Analyze, Implement and Control).
- Organize your time
Businesses that use the Lean Six Sigma technique will be able to assist their staff in effectively managing their time, resulting in more efficient operations and more productive employees than ever before.
- Employee motivation and satisfaction
Employee happiness and motivation are critical for a business’s success since it requires the workforce to behave and respond appropriately – but employees will only be required to do so if they are sufficiently motivated. Providing your staff with Six Sigma training will enable them to learn new skills and techniques, allowing them to advance their careers and create a positive work environment that results in highly satisfied employees with greater motivation.
- Planning for the future
Six Sigma is more than simply a process optimization methodology; it also serves as a strategic planning tool at the corporate level. The strategies and tactics you create and apply in your business are critical because they are the aspects that will help you achieve your goals in the most efficient and effective manner possible.
Watch this video: Six Sigma Green Belt Introduction
Wrapping up
Enterprises must accommodate the demands of complicated business needs in today’s service-based economy, and Six Sigma can be a powerful and strategic process improvement approach in this regard to maintain consistency in its performance. This shift in culture brought about by the implementation of Lean Six Sigma can be viewed as a foundation for enhanced performance and operational excellence. Achieving a Lean Six Sigma Certification is one of the most effective ways to do so.
SKILLOGIC is a global provider of IT consultancy and professional certification training with offices in more than 30 countries. We provide Six Sigma courses such as Six Sigma Green Belt Training, Six Sigma Black Belt Training, and Six Sigma Combo Training, which combines both Green and Black Belt training under one roof. International organizations like ICFQ and TUV have both accredited our courses.
You can check this – Six Sigma Certification Cost in 2022
Watch this video: Six Sigma Black Belt Training Introduction
0
12351