Quality Manager - Job Descriptions, Salaries, and Skills Required
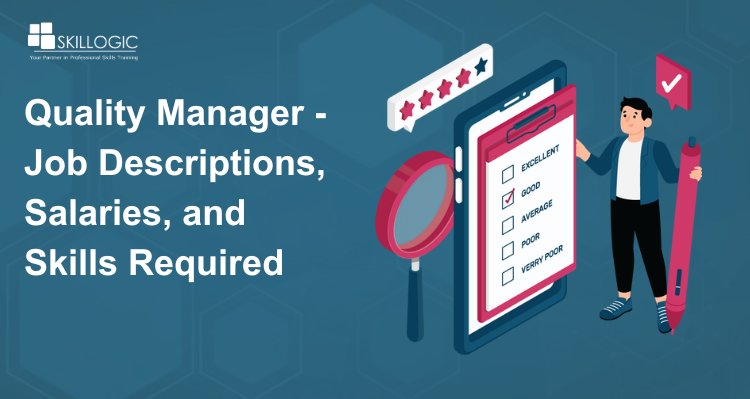
All industries' businesses are constantly aiming to be the best. When combined with the best practices and procedures to do so successfully and efficiently, their greatest products or services aid in creating a devoted customer base.
Prior to launch, quality management is a crucial tool for attaining the greatest results for your business. Businesses may guarantee consistent excellence in their products and services by a continuous process of managing, monitoring, and improving quality.
In this article, we will learn who a quality manager is, what is the salary of a quality manager, what are the skills required to be a quality manager and many more.
Who Is a Quality Manager?
Quality management is an essential tool for achieving the best outcomes for your company before launch. Companies can maintain quality in their offers and services and maintain a competitive advantage by continuously controlling, monitoring, and enhancing productivity.
Due to the need of providing high-quality products and services that increase client bases in today's competitive global market, more businesses are now implementing quality management methods for their enterprises.
The quality manager, also known as the quality assessment manager, inspects the finished product to make sure it was produced in line with legal requirements and determines whether it meets consumer expectations. A top-notch quality manager should be diligent and vigilant.
What is Quality
What Does a Quality Manager Do?
Out of practically all employees, quality managers must be some of the most specific and detail-oriented persons. After all, the caliber of a product can either propel a business to the next level or lead to its demise. This position requires utter focus on detail at all times.
Managers of quality play a crucial role in overseeing production processes and ensuring the overall quality of products. They are responsible for conducting thorough checks, implementing quality control tests, and generating reports for higher-level management. Obtaining a Six Sigma Black Belt certification is a valuable addition to their skill set, as it equips them with advanced tools and methodologies to optimize processes and enhance product development procedures. This certification signifies expertise in quality management and process improvement, enabling managers to contribute significantly to the overall efficiency and excellence of a business's operations.
Refer to these articles:
Requirements To Be a Quality Manager
- Business administration degree or a related field.
- Certification for quality control is advantageous.
- Excellent detail-orientedness
- Outstanding written and verbal communication.
- Statistical knowledge and data analysis skills.
- Strong interpersonal abilities.
- Highly conscientious and hardworking.
Job Description Of a Quality Manager
A quality manager, responsible for developing and implementing procedures to ensure product quality, including inspections and assessments, is often referred to as a quality assurance manager. They meticulously examine information on inspections and production line cleanliness, preparing detailed reports. A top-notch quality manager is conscientious and watchful. Six Sigma certification training enhances their skills in process improvement and quality management.
A Quality manager must feel responsible to both present and potential customers and must be well-versed in the production's specifications.
Skills Required To Be a Quality Manager?
The skills and expertise needed from a quality manager are as follows:
- To present their findings to the business leadership and production management.
- All stages of the production process should be covered in training for quality assurance for the workforce.
- Ensuring that goods or services are checked to see if they fulfill quality requirements.
- Set up meetings with production or service management to find out more about the procedures used by the company.
- Should have extensive manufacturing management expertise and strong business management skills.
Quality managers should be meticulous in their job, great meeting planners and managers, and possess leadership skills.
Read these following articles:
- How much does the Lean Six Sigma Certification Cost in Mumbai?
- How much does the Lean Six Sigma Certification Cost in Hyderabad?
- How much does the Lean Six Sigma Certification Cost in Kolkata?
Responsibilities Of a Quality Manager?
Based on the industry, size of the company, and internal corporate requirements, the responsibilities in this position will change. Some of the regular tasks include:
- Analyzing consumer feedback and determining what the public wants and expects from products and services
- Controlling production waste and enhancing the effectiveness of production procedures
- Establishing quality-focused production plans for new products
- Using a range of stress tests to evaluate a product's or service's quality
- Collaborating with management teams to offer suggestions and remedies for quality problems
- Reporting on the quality of goods and/or services at all production stages
- Evaluating and examining all supplies given by vendors to guarantee overall quality
- Investigating the underlying causes of faults and making recommendations for fixes
- Orienting and training new employees of the quality control team
- Keeping up with new quality control methods and techniques
Salary Of a Quality Manager
The experience level has the biggest impact on compensation. Certainly, your salary will increase as you get more experience .The average yearly income for a quality manager in India is ₹8 lakhs, with salaries ranging from ₹3.0 lakhs to ₹20.0 lakhs.
Read these articles:
- What is the Six Sigma Certification Cost in Bangalore
- How much does the Lean Six Sigma Certification Cost in Chennai?
- How much does the Lean Six Sigma Certification Cost in Pune?
Sectors Where Qualified Managers Are Required
It's not surprising that organizations from a wide range of industries rely on quality managers to create top-notch products and services within their operations given the focus on maintaining a high level of perfection.
Top sectors for hiring competent managers include:
- Healthcare and Pharmaceutical
- Manufacturing
- Financial Institutions
- Food and Beverage
- Legal Organizations
- Government Departments
Final Words
With the emphasis on maintaining top-tier perfection, it is not unexpected that businesses from a wide range of industries rely on qualified executives to deliver top-tier goods and services throughout their operations.
In order to increase internal high-quality consistency, a quality manager is also responsible for overseeing training and implementing any necessary process adjustments.Since it offers many opportunities to ensure that goods and services are produced consistently to boost production, quality management is one of the most fascinating careers for aspirants.
With SKILLOGIC's Lean Six Sigma Expert, Lean Six Sigma Green Belt Certification Training, and Post Graduate Program in Lean Six Sigma, you may become a quality expert. By enhancing quality and outcomes, this Lean Six Sigma certification program from SKILLOGIC Institute enables you to develop essential leadership abilities for operational excellence in transformational initiatives.
This course focuses on Lean methods and Six Sigma, two critical management methodologies that help speed up corporate improvement.
What is Six Sigma
Six Sigma Green Belt Introduction
Six Sigma Black Belt Training Introduction
0
258