Exploring Essential Six Sigma Tools for Process Improvement
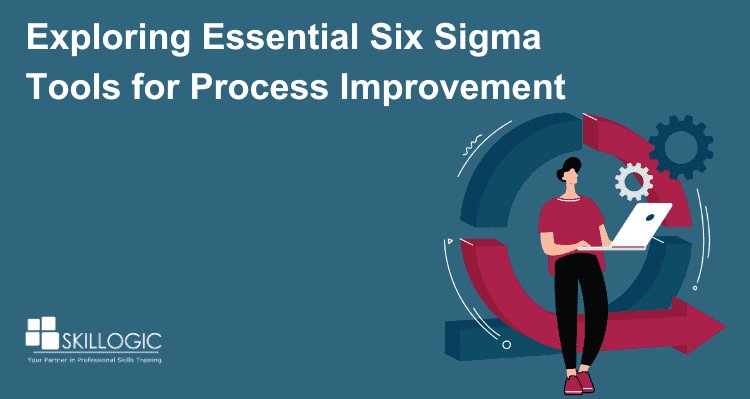
In today's competitive world, every business aims to improve its processes to deliver better quality products and services. That's where Six Sigma comes in. In this article, we'll explore the essential tools of Six Sigma, which help businesses find and fix problems in their operations. These tools are like a toolkit for making things run smoother and better. We'll break down each tool, explaining how it's used and why it's important. By the end, you'll have a clear understanding of how Six Sigma Tools can help businesses achieve their goals of improvement and excellence.
Understanding Six Sigma
The global market for quality management software reached USD 8.68 billion in 2021. Projections indicate substantial growth, with an estimated value of USD 20.83 billion by 2030. This growth trajectory reflects a compound annual growth rate (CAGR) of 10.48% anticipated between 2022 and 2030. Quality management software plays a pivotal role in implementing Six Sigma methodologies effectively. By leveraging advanced analytics and process optimization tools, organizations can enhance their quality control mechanisms, driving efficiency and minimizing defects.
Six Sigma is a methodology aimed at minimizing defects and variations in processes to improve quality and efficiency. Its core principle is to achieve near-perfection by reducing defects to a level of no more than 3.4 per million opportunities. This approach involves a systematic process improvement methodology known as DMAIC:
- Define: This phase involves defining the problem or opportunity for improvement, clarifying project goals, and establishing project scope.
- Measure: In this phase, relevant data is collected and measured to quantify the current performance of the process and identify areas for improvement.
- Analyze: The data collected is analyzed to identify the root causes of defects or variations in the process, using tools such as histograms, Pareto charts, and cause-and-effect diagrams.
- Improve: Based on the analysis, solutions are developed and implemented to address the root causes of defects, aiming to optimize the process and improve quality.
- Control: In the final phase, control measures are established to sustain the improvements achieved, monitoring the process to ensure that it remains stable and within acceptable limits.
By following the DMAIC framework, organizations can systematically identify and address process inefficiencies, leading to enhanced quality, increased customer satisfaction, and improved overall performance.
The Significance of Tools in Six Sigma:
Tools play a pivotal role in the successful implementation of six sigma methodologies, enabling organizations to effectively identify, analyze, and improve their processes. These tools facilitate data-driven decision-making and process optimization in the following ways:
Data Collection and Analysis: Six Sigma tools provide structured methods for collecting and analyzing data related to process performance, defects, and variations. By utilizing tools such as histograms, control charts, and scatter plots, organizations can gain valuable insights into the root causes of problems and make informed decisions based on empirical evidence.
Root Cause Analysis: Many tools in six sigma, such as cause-and-effect diagrams and fishbone diagrams, help identify the underlying factors contributing to process defects or variations. By systematically analyzing these factors, organizations can pinpoint the root causes of problems and develop targeted solutions to address them.
Process Visualization: Tools like process maps and flowcharts enable organizations to visualize their processes and identify areas of inefficiency or waste. This visualization helps stakeholders understand the flow of work, identify bottlenecks, and prioritize improvement efforts for maximum impact.
Statistical Analysis: Tools in six sigma include a variety of statistical techniques, such as regression analysis, hypothesis testing, and analysis of variance (ANOVA), which enable organizations to quantify the relationship between process inputs and outputs. By applying statistical methods, organizations can validate hypotheses, identify significant factors influencing process performance, and make data-driven decisions to optimize processes.
Continuous Improvement: Six Sigma tools support organizations in their pursuit of continuous improvement by providing mechanisms for monitoring process performance over time. Control charts, for example, enable organizations to track key process metrics and detect any deviations from the desired performance levels. This proactive monitoring allows organizations to take corrective actions promptly and maintain process stability and consistency.
Read these articles:
Exploring Key Tools in Each Phase of the DMAIC Framework
Define Phase:
- SIPOC (Supplier, Input, Process, Output, Customer) Diagram: Helps define the scope of the project by identifying key elements of the process, including suppliers, inputs, processes, outputs, and customers. This tool provides a high-level overview of the process flow and identifies stakeholders involved.
- Voice of Customer (VOC) Analysis: Gathers and analyzes customer feedback and requirements to understand their needs, preferences, and expectations. VOC analysis helps align project goals with customer expectations, ensuring that improvement efforts focus on delivering value to the customer.
Measure Phase:
- Process Mapping: Visualizes the sequence of steps in a process to identify activities, inputs, outputs, and interactions. Process mapping helps stakeholders understand the current state of the process and identify areas for measurement and improvement.
- Cause-and-Effect Diagram (Fishbone Diagram): Structured brainstorming tool that identifies potential causes of a problem or defect. By categorizing factors such as people, methods, machines, materials, measurements, and environments, the Fishbone Diagram helps teams identify root causes that contribute to process variations.
- Measurement System Analysis (MSA): Evaluates the reliability and accuracy of measurement systems used to collect data. MSA assesses measurement equipment, operators, and procedures to ensure that data collected is accurate and consistent, minimizing measurement error.
Analyze Phase:
- Histograms: Visual representation of data distribution, showing the frequency and distribution of values. Histograms help identify patterns, trends, and variations in process data, facilitating further analysis and decision-making.
- Pareto Charts: Prioritizes the most significant factors contributing to defects or problems by ranking them in descending order of frequency or impact. Pareto Charts help focus improvement efforts on the vital few factors that have the most significant impact on process performance.
- Scatter Plots: Graphical representation of the relationship between two variables, showing the correlation or lack thereof. Scatter plots help identify potential cause-and-effect relationships between process inputs and outputs, guiding further analysis and investigation.
- Root Cause Analysis: Structured procedure for pinpointing the root causes of issues or flaws. Root cause analysis involves techniques such as 5 Whys, Ishikawa Diagrams, and fault tree analysis to identify and address root causes effectively.
Improve Phase:
- Design of Experiments (DOE): Statistical technique for systematically changing process inputs to identify the optimal settings for achieving desired outputs. DOE helps optimize process performance by identifying the most influential factors and their interactions.
- Failure Mode and Effects Analysis (FMEA): Proactive risk assessment tool that identifies potential failure modes in a process, evaluates their severity, occurrence, and detection, and prioritizes mitigation actions. FMEA helps prevent and mitigate process failures before they occur, reducing the risk of defects and errors.
- Pilot Testing: Small-scale implementation of improvement ideas or changes to evaluate their effectiveness before full-scale implementation. Pilot testing helps validate improvement hypotheses, identify potential issues, and refine solutions before wider deployment.
Control Phase:
- Control Charts: Statistical tool for monitoring process performance over time by plotting data points and control limits. Control charts help distinguish between common cause and special cause variation, enabling timely corrective actions to maintain process stability and consistency.
- Standard Operating Procedures (SOPs): Detailed instructions for performing routine tasks consistently and efficiently. SOPs provide guidelines for process execution, ensuring that activities are performed uniformly and in accordance with best practices.
- Statistical Process Control (SPC): Methodology for monitoring and controlling process variation using statistical techniques. SPC involves establishing control limits, measuring process performance, and taking corrective actions to maintain process stability and meet quality objectives.
By leveraging these key tools in each phase of the DMAIC framework, organizations can systematically identify, analyze, and improve their processes, driving continuous improvement and achieving sustainable results.
Refer to these articles:
- Six Sigma Certification Cost in India
- Why Six Sigma Certification in India?
- PMP Certification Cost in India
Case Studies and Examples: Unveiling Six Sigma in Action
Toyota:
Tool Highlighted: Value Stream Mapping
Toyota implemented Six Sigma methodologies, including Value Stream Mapping, to identify and eliminate waste in their production processes. By streamlining their supply chain and production lines, Toyota achieved significant cost savings and improved efficiency, leading to higher customer satisfaction.
General Electric (GE):
Tool Highlighted: Design of Experiments (DOE)
GE utilized Six Sigma tools such as Design of Experiments to optimize their manufacturing processes. By systematically varying process inputs and analyzing their effects on output variables, GE was able to identify the optimal settings for improving product quality and reducing defects, resulting in substantial cost savings and increased profitability.
Motorola:
Tool Highlighted: Statistical Process Control (SPC)
Motorola implemented Statistical Process Control (SPC) as part of their Six Sigma initiative to monitor and control variations in their manufacturing processes. By using control charts to track process performance over time, Motorola was able to detect and address deviations from desired standards, leading to improved product quality and reliability.
Amazon:
Tool Highlighted: Root Cause Analysis
Amazon utilized Six Sigma tools such as Root Cause Analysis to identify and address issues in their fulfillment centers. By analyzing data on order processing times and shipment accuracy, Amazon was able to pinpoint the root causes of delays and errors, implementing corrective actions to improve operational efficiency and customer satisfaction.
Healthcare Industry:
Tool Highlighted: Failure Mode and Effects Analysis (FMEA)
A healthcare organization implemented Six Sigma methodologies, including Failure Mode and Effects Analysis (FMEA), to enhance patient safety and quality of care. By proactively identifying potential failure modes in clinical processes and implementing preventive measures, the organization reduced medical errors and improved patient outcomes.
These case studies demonstrate the diverse applications of Best Six Sigma Tools across different industries and highlight the tangible benefits achieved through their successful implementation. By leveraging specific tools to address process challenges and drive continuous improvement, organizations can achieve significant improvements in quality, efficiency, and customer satisfaction.
Refer to this article: Who Is a Quality Manager?
Optimizing Six Sigma Implementation: Best Practices for Harnessing Tools and Driving Results
Implementing Six Sigma tools effectively is crucial for driving meaningful process improvement and achieving desired outcomes. Here are some recommended strategies to guarantee the effective execution:
Gain Leadership Support and Commitment:
- Secure buy-in from senior management and ensure their active involvement in the Six Sigma initiative.
- Communicate the benefits of Six Sigma tools in terms of improved quality, reduced costs, and enhanced customer satisfaction.
- Allocate resources, including budget, time, and personnel, to support the implementation of six sigma projects.
Provide Comprehensive Training for Employees:
- Offer six sigma training programs on Six Sigma methodologies and tools to equip employees with the necessary skills and knowledge.
- Tailor training sessions to the specific needs and roles of different employee groups, ensuring relevance and applicability.
- Provide ongoing education and support to reinforce learning and facilitate the successful application of Six Sigma tools in daily work.
Foster a Culture of Continuous Improvement:
- Create a supportive environment that encourages employees to embrace change and actively participate in improvement initiatives.
- Recognize and reward employees for their contributions to Six Sigma projects and process improvement efforts.
- Establish clear goals and metrics to measure the effectiveness of Six Sigma tools and track progress over time.
Promote Data-Driven Decision-Making:
- Emphasize the importance of collecting, analyzing, and using data to drive decision-making and problem-solving.
- Provide access to relevant data and tools for data analysis, empowering employees to make informed decisions based on evidence.
- Encourage collaboration and knowledge sharing among team members to leverage collective insights and expertise.
Encourage Cross-Functional Collaboration:
- Foster collaboration and communication across different departments and functions to break down silos and facilitate holistic problem-solving.
- Encourage cross-functional teams to work together on Six Sigma projects, leveraging diverse perspectives and expertise.
- Establish clear roles and responsibilities for team members, ensuring accountability and alignment with project objectives.
The adoption of Six Sigma tools is crucial for organizations aiming for quality, efficiency, and customer satisfaction. By understanding and using these tools, businesses identify improvement opportunities, optimize processes, and drive sustainable results. Embracing a culture of continuous improvement and data-driven decision-making, with strong leadership support, ensures Six Sigma methodologies are ingrained in the organizational DNA, fostering long-term success. SKILLOGIC offers accredited Six Sigma Courses recognized by institutions like ICFQ and TUV, providing professionals with the knowledge, skills, and certifications to excel in quality management.