What includes in the 5 S of Six Sigma?
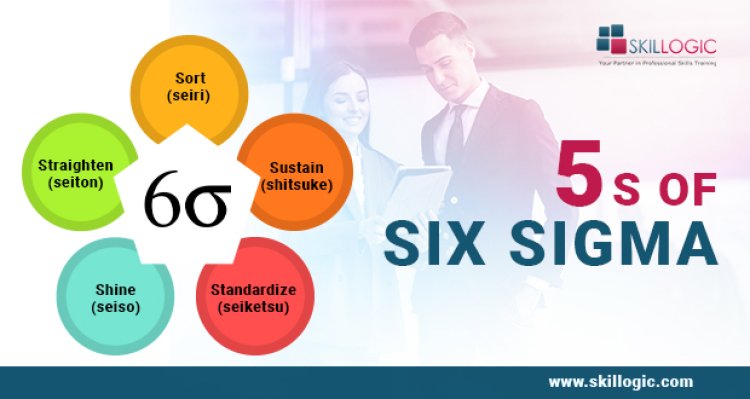
In this world where 2.5 quintillion bytes of data is being created every day, formulating the right predictions can help foretell problems affecting the entire organization. With so many ideas being put forth, implementing the right one is important. No one knows what the next day holds, so we cannot overstate the importance of being able to make predictions. Six Sigma aids businesses to increase the veracity and authenticity of the decision-making process.
What is Six Sigma?
Six Sigma is a data-driven procedure that produces tools and techniques to draw and assess each step within a process. It has the potential to upgrade performance and reduce process inconsistencies.
Six Sigma Use Cases:
Six Sigma epitomizes a management ideology that centers around supplementing statistical improvements to a business process. It champions qualitative measurements of success more than qualitative markers. Hence, professionals of Six Sigma are business people who apply statistics, financial analysis, and project management techniques to establish advanced business functionality.
Some of them are:
- Raise Customer Satisfaction levels
- Raise in Revenue
- Scaled-down cost
- Decreased Process variation
- Refine and revamp Employee morale
- Boost participation and ownership
What are the Six Sigma Principles?
Six sigma functions by keeping these principles in check:
For a business to succeed there should be consistent attempts to acquire stable and predictable process results.
Manufacturing and business operations possess features that can be specified, studied, examined, enhanced, and managed.
Accomplishing prolonged quality improvement needs commitment from the entire organization.
All processes can be interpreted and examined in detail, and consequently, be improved: if you control the inputs, you can control the outputs.
Let’s Understand the 5 S of Six Sigma:
5 S is a structure to minimize waste and optimize productivity by nurturing a workplace that is spick and span. It also uses visual cues to secure congruous operational results. 5 S works by “cleaning up” and “sorting out” the workplace primarily, in its existing configuration, and it is normally the first lean method that organizations perform.
The five S method helps the workplace to get rid of items that are no longer necessary(sort), systematize the items to enhance productivity and flow (straighten), clean the area such that any further problems could be easily identified(shine), discharging color coding and labels to stay compatible with other areas (standardize) and expand behaviors that keep the workplace organized over the long term (sustain).
The 5S pillars, Sort (Seiri), Set in Order (Seiton), Shine (Seiso), Standardize (Seiketsu), and Sustain (Shitsuke), supply a procedure for assembling, cleaning, initiating, and bolstering a productive work environment.
- Sort (seiri) – Sorting is differentiating between necessary and unnecessary things, and chucking away what you do not need. Here, we expel superfluous items from the workplace that are unwanted for current production operations.
- Straighten (seiton) – Straightening is the procedure of ordering and organizing the items so that the right item can be picked effectively at the right time, and it will come in handy for everyone. When there is a definite place for everything, the available ones will be put to use without any waste. Straightening is the process of cleaning the work area of its chaotic nature.
- Shine (seiso) – Shine as in designing and producing a clean worksite without any garbage, dirt, and dust. This will enable businesses to identify the problems within their workspace which were unnoticed such as leaks, spills, excess damage etc.
- Standardize (seiketsu) – As the name suggests, here businesses establish standards for a neat, clean, workplace. Standardization centers around ‘visual management. It will make any irregularity known to management.
- Sustain (shitsuke) – It is extremely strenuous to properly maintain correct procedures. Establishing behaviors and habits to keep up with the accepted standards over the long term, and modeling the workplace organization as the cue to managing the process for success.
How is Six Sigma Beneficial?
- Minimize waste generation from spills and clean-up
- Environmental benefits (e.g., avoided materials, wastes, and energy needed to produce the defective output; avoided the need to dispose of defective output).
- Reduce Operational Costs
- Bring efficacy and efficiency to the businesses
- Reduce legal risks if any
- Improved Customer Services
Let’s Wrap up:
Six Sigma is a method employed to update business processes by utilizing statistical analysis. Processes are advanced by controlling variation and comprehending the intricacies within them. This effect is a more predictable and profitable business process.
Six Sigma is above and beyond “training”; it is a perspective based on data and adapts to projects and produces qualitative business outcomes. The approach has proven its vitality and is implemented within a wide range of industries that are striving to achieve both hard and soft money savings while increasing customer satisfaction.
Wish to step into the world of Six Sigma? The first step for that is getting training on the Six Sigma Course from SKILLOGIC that is accredited by ICFQ and TUV. Score success with SKILLOGIC.
0
5257