Quality Management Vs. Quality Assurance
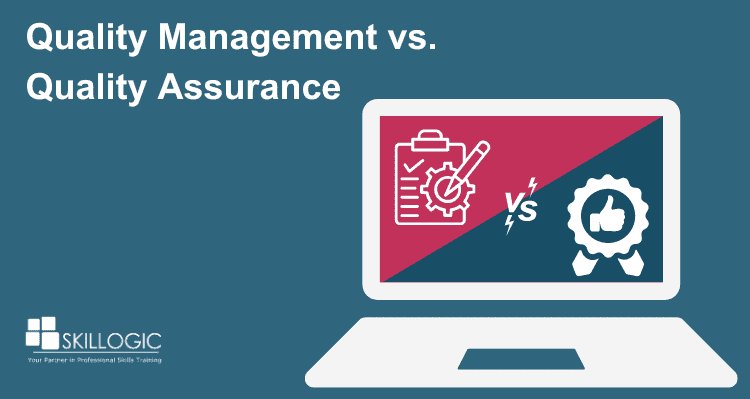
In today's competitive business landscape, ensuring quality is not just a goal but a necessity for sustainable success. Whether in manufacturing, service industries, or software development, maintaining high standards is key to meeting customer expectations and staying ahead of the competition. Two terms often used interchangeably but with distinct meanings are Quality Management (QM) and Quality Assurance (QA). Understanding the nuances between these concepts is crucial for organizations striving for excellence.
According to research from Straits Research, the global market for quality management software was valued at USD 8.68 billion in 2021. Projections indicate that this figure is set to surge to USD 20.83 billion by 2030, indicating a robust compounded annual growth rate (CAGR) of 10.48% over the forecast period from 2022 to 2030. Let's delve into each of these disciplines and explore their significance in ensuring product and service quality.
Exploring the Essence of Quality Management
Quality management is a comprehensive approach to ensuring that products, services, and processes consistently meet or exceed customer expectations. It encompasses a range of techniques, methodologies, and principles aimed at achieving excellence in all aspects of an organization's operations. By focusing on quality, businesses can enhance customer satisfaction, improve efficiency, reduce costs, and ultimately gain a competitive edge in the marketplace.
According to a report by Polaris Market Research, the market size of Quality Management Software soared to USD 9.92 billion in 2023. Projections indicate further growth, with the market expected to reach USD 10.83 billion in 2024 and surge to a substantial USD 24.92 billion by 2032. This trajectory reflects a notable compound annual growth rate (CAGR) of 11.0% throughout the forecast period.
In recent years, the importance of quality management has surged as organizations recognize its critical role in achieving success and sustainability. With globalization, increasing competition, and rising customer expectations, businesses across industries are prioritizing quality management to maintain relevance and thrive in dynamic markets.
Moreover, advancements in technology, such as artificial intelligence, data analytics, and automation, have revolutionized quality management practices, enabling organizations to streamline processes, identify defects, and drive continuous improvement with unprecedented precision and efficiency, leveraging Six Sigma Green Belt training.
Delving into the Depths of Quality Assurance
Quality assurance is a systematic process designed to ensure that products, services, and processes meet predetermined quality standards and requirements. It involves establishing quality checkpoints, conducting inspections and audits, and implementing corrective actions to maintain consistency and uphold customer satisfaction. Quality assurance plays a vital role in enhancing product reliability, mitigating risks, and fostering trust between businesses and their customers.
According to Verified Market Reports, the Global Quality Assurance Service Market is forecasted to reach a valuation of USD 7.29 billion by 2026, with a projected compound annual growth rate (CAGR) of 11.2% from 2019 to 2026.
In recent years, quality assurance, bolstered by methodologies like Lean Six Sigma certification, has gained significant traction across industries as organizations recognize its pivotal role in delivering high-quality products and services. With increasing competition and evolving customer expectations, businesses are prioritizing quality assurance to differentiate themselves and build a loyal customer base. Moreover, advancements in technology, such as automation, artificial intelligence, and data analytics, have revolutionized quality assurance practices, enabling organizations to streamline processes, detect defects more efficiently, and drive continuous improvement with greater precision and effectiveness.
Read these articles:
Key Differences Between Quality Management and Quality Assurance
Quality Management and Quality Assurance are two important concepts in ensuring the quality of products or services in any organization. Here are the key differences between them:
Scope:
- Quality Management: Quality management involves a broader scope, covering all aspects of the organization's operations, including planning, manufacturing, marketing, and customer service.
- Quality Assurance: Quality assurance is more focused, primarily concerned with the processes involved in creating the product or service.
Focus:
- Quality Management: Quality management focuses on meeting customer requirements and continuously improving processes and products/services.
- Quality Assurance: Quality assurance focuses on establishing standards and procedures to prevent defects and ensuring that the processes are being followed correctly.
Implementation:
- Quality Management: Quality management involves the integration of quality-related activities throughout the organization, involving all employees in the process.
- Quality Assurance: Quality assurance activities are typically carried out by dedicated quality assurance teams or departments within the organization.
Responsibility:
- Quality Management: Quality management is the responsibility of all members of the organization, from top management to front-line employees.
- Quality Assurance: Quality assurance is the responsibility of the quality assurance team or department, which monitors and audits processes to ensure compliance with standards.
Outcome:
- Quality Management: The outcome of quality management is overall improvement in the organization's performance and customer satisfaction.
- Quality Assurance: The outcome of quality assurance is the prevention of defects and ensuring that products or services meet specified standards and requirements.
Continuous Improvement:
- Quality Management: Quality management emphasizes continuous improvement through methods such as PDCA (Plan-Do-Check-Act) or Six Sigma.
- Quality Assurance: Quality assurance focuses on ensuring that processes are consistent and repeatable, with less emphasis on continuous improvement initiatives.
Benefits of Effective Quality Management and Quality Assurance
Quality management and quality assurance are crucial aspects of ensuring products or services meet or exceed customer expectations. Here are the benefits of each
Quality Management:
- Consistency: Implementing effective quality management ensures consistency in processes, leading to consistent product or service quality.
- Customer Satisfaction: By focusing on quality management, organizations can consistently meet customer requirements and expectations, resulting in higher satisfaction levels.
- Cost Reduction: Quality management practices identify and eliminate inefficiencies and defects, leading to cost reductions associated with rework, scrap, and warranty claims.
- Improved Processes: Quality management emphasizes process improvement, leading to streamlined operations, increased productivity, and enhanced competitiveness.
- Risk Mitigation: It helps in identifying potential risks in processes and products early on, allowing organizations to mitigate these risks before they escalate into larger issues.
- Employee Engagement: Engaged employees are often key to quality management success, as they are actively involved in process improvement efforts and feel a sense of ownership over quality outcomes.
- Enhanced Reputation: Consistently delivering high-quality products or services builds a positive reputation in the market, leading to increased trust and brand loyalty.
Quality Assurance:
- Preventive Approach: Quality assurance focuses on preventing defects rather than detecting and correcting them afterwards, leading to higher overall product or service quality.
- Compliance: It ensures that products or services meet regulatory and industry standards, reducing the risk of non-compliance penalties and legal issues.
- Standardization: Quality assurance establishes standard procedures and protocols, ensuring consistency in product or service delivery across different teams or locations.
- Early Issue Identification: By implementing quality assurance measures, organizations can identify issues early in the production or service delivery process, minimizing their impact on final output.
- Customer Confidence: Quality assurance practices instil confidence in customers regarding the reliability and consistency of products or services, contributing to long-term customer relationships.
- Continuous Improvement: Quality assurance is not a one-time activity but an ongoing process, encouraging continuous improvement and adaptation to changing customer needs and market conditions.
- Data-Driven Decision-Making: Quality assurance relies on data and metrics to assess performance and identify areas for improvement, enabling informed decision-making at all levels of the organization.
Challenges and Best Practices of Quality Management and Quality Assurance
Here are the challenges and best practices of quality management and quality assurance defined in points:
Challenges of Quality Management:
- Resistance to Change: Implementing new quality management practices can face resistance from employees accustomed to existing processes.
- Lack of Leadership Support: Without strong leadership commitment, it's challenging to drive the necessary cultural and procedural changes for effective quality management.
- Resource Constraints: Limited resources, including financial, human, and technological, can hinder the implementation of comprehensive quality management systems.
- Complex Supply Chains: Managing quality across complex supply chains poses challenges in ensuring consistency and adherence to standards.
- Inadequate Training: Insufficient training programs can lead to inconsistent understanding and application of quality management principles among employees.
Best Practices of Quality Management:
- Leadership Commitment: Top-level management should demonstrate a clear commitment to quality management by allocating resources, setting objectives, and actively participating in improvement initiatives.
- Continuous Improvement: Establishing a culture of continuous improvement encourages employees to identify and address quality issues proactively.
- Employee Involvement: Involving employees in quality management processes empowers them to contribute ideas, identify problems, and take ownership of quality outcomes.
- Data-Driven Decision Making: Utilizing data analytics and metrics enables organizations to make informed decisions, identify trends, and prioritize improvement efforts.
- Supplier Collaboration: Collaborating closely with suppliers to establish quality standards, conduct audits, and provide feedback fosters a mutually beneficial relationship and ensures consistency in product or service quality.
Challenges of Quality Assurance:
- Changing Requirements: Adapting to evolving customer requirements and market trends poses challenges in maintaining consistency in quality assurance processes.
- Technological Advances: Incorporating new technologies and tools for quality assurance requires investment in training and may disrupt existing workflows.
- Regulatory Compliance: Ensuring compliance with industry regulations and standards adds complexity to quality assurance efforts, particularly in highly regulated sectors such as healthcare and aerospace.
- Globalization: Operating in global markets introduces challenges related to cultural differences, language barriers, and varying quality standards across regions.
- Cost Pressure: Balancing the need for rigorous quality assurance with cost constraints can be challenging, particularly for organizations operating in competitive markets.
Best Practices of Quality Assurance:
- Standardized Processes: Establishing standardized processes and procedures for quality assurance promotes consistency and repeatability in product or service delivery.
- Risk Management: Implementing robust risk management practices enables organizations to identify potential quality issues early and mitigate them effectively.
- Automated Testing: Leveraging automated testing tools and techniques accelerates the testing process, improves accuracy, and reduces the likelihood of human error.
- Cross-Functional Collaboration: Encouraging cooperation amongst several departments, including operations, testing, and development, makes a comprehensive approach to quality assurance possible.
- Continuous Monitoring: Implementing systems for continuous monitoring and feedback allows organizations to detect deviations from quality standards promptly and take corrective actions.
The importance of understanding the distinction between Quality Management and Quality Assurance cannot be overstated. While both are essential components of ensuring product and service quality, they serve different purposes within an organization. Encourage businesses to invest in robust Quality Management and Assurance practices as a strategic imperative for achieving excellence and sustaining long-term success in today's competitive landscape. Additionally, consider integrating a Six Sigma Black Belt course to enhance proficiency in quality management methodologies and drive continuous improvement efforts.
Refer to these articles:
- Six Sigma Certification Training Course Cost in India
- PMP Certification Training Course Cost in India
- Why Six Sigma Certification in India?
Prospective learners have the option to enrol at SKILLOGIC Institute, a prestigious global training institution renowned for its specialized certification programs in Project Management, Quality Management, Cyber Security, Software Development, and Business Analytics. With over a decade of experience, SKILLOGIC® stands out as a leader in the industry, catering to a diverse international student base of over 100+ learners. Offering a comprehensive array of more than 25 accreditations and partnerships, supported by a dedicated team of over 100 experienced instructors, SKILLOGIC Institute provides unmatched opportunities for professional growth and development.
0
302