What is Zero Defect in Quality Management?
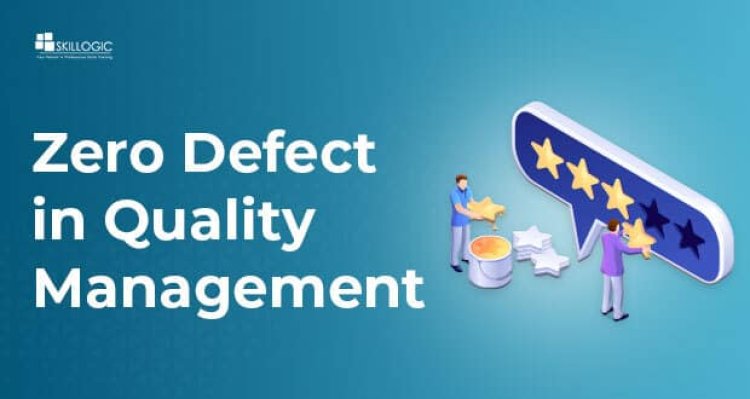
Striking for Zero Defects is a noble goal, and most businesses find that the benefits exceed the drawbacks. Organizations can enhance their current processes, construct better processes, and create an environment of continuous improvement by striving for astringent (but feasible) reduction of faults.
Although implementing zero faults can be difficult, the advantages are well worth the effort. We’ll look at what zero-defect is and how it may help your company succeed in this blog post.
What is zero-defect?
In quality management, zero defects refer to a company’s aim to assure that all items leaving its facility are defect-free. Companies can do this by implementing detailed planning and employing diligent personnel who are continuously on the lookout for mistakes.
Zero faults is a quality management concept that refers to the release of products and services with no discrepancies. Its goal is to reduce the defect rate in manufactured products and services to the absolute minimum. Let’s have a look at the concept of Zero Defects.
The Zero Defects method considers prevention to be the most important quality principle. The cost of failing to achieve the criteria serves as a quality standard. Zero Defects should be seen as the goal of delivering products that are free of faults or executing processes that are free of errors.
It means that if a simple product meets the first requirements, it is a quality product. That is, if it meets the customer’s needs, it’s only reasonable to declare it meets quality standards and has (almost) zero flaws.
Subsequent defects and difficulties are prevented, and overall product or service quality is enhanced, by addressing the root cause of the defect quickly and not accepting or passing on defects. In all reality, it means getting it right the veryfirst time.
Principles of Zero Defect:
Quality is essential to ensure that all of the critical aspects of manufacturing are addressed, allowing for efficient processes and procedures.
Quality must be given equal consideration and corrected. It is incomprehensible that the corporation begins with manufacturing and then attempts to determine quality standards. The number of problems found must be kept to a minimum. If not, the cost of putting things right will be enormous for the company.
Money is spent on quality. To compare the statistics, the company must calculate its waste, production, and revenues in monetary terms.
The company must have zero flaws as its goal and strive for excellence, despite the fact that it is practically impossible to achieve.
What are the benefits of Zero Defect?
- It boosts worker morale and increases consumer perception.
The mindset of “we’re going to make mistakes regardless” should be avoided at all costs, as it can be detrimental to an organization’s productivity. Despite this, it’s quite common today, particularly in the computer field. Many specialists in this field believe it is difficult to execute their professions without a considerable margin of error, which can quickly erode team morale without anybody knowing.
- It gets rid of the concealed expenditures.
Many businesses mistakenly believe that a new product’s development costs finish when it is released to the market. However, anyone who has had to maintain something for several months knows that this is far from the case. On the one hand, zero faults can help you get away from that troublesome situation to some level, while on the other hand, it can make it much more evident what additional expenses you’re suffering from post-release maintenance and how to avoid them.
- Customer interaction is improved.
Customers will be thrilled and will return if the product is of higher quality. At the end of the day, this translates to long-term client connections and increased company profitability. However, the company must guarantee that the tight environment developed to secure zero faults does not result in low employee morale.
- Boosts employee morale
Workers frequently believe that little errors will occur while they are working. The zero-defect idea, on the other hand, shifts workers’ mindsets and motivates them to work without making any mistakes. This boosts employee morale.
Refer To The Article What is the Lean Six Sigma Control Plan?
How do you go about implementing zero-defect?
- Determine which quality concerns are costing you the most money.
- The company must first recognise the appropriate way to conduct things in order to identify the adjustments that need to be made in the process.
- Recognize the quality requirements of your customers. Make every effort to meet it.
- Motivating, promising, challenging, emphasising the value of teamwork, and rewarding people are all ways in which the corporation can push its staff to produce high-quality products.
- For quality enhancement, assemble a qualified team.
- “Prevention is better than cure,” we all know. It is preferable to avoid mistakes by implementing strong design mechanisms that do not allow for errors.
- Keep a close eye on your process so you can pinpoint the source of the problem and take appropriate action.
- Take corrective steps to eliminate the causes of the defect.
- Continue to do all of these things in order to attain zero defects.
Also Read: What are the Six Sigma Levels and Why Do We Need to be Certified?
Conclusion
Continue to do all of these things in order to attain zero defects. Quality control is a method of lowering the number of defective items. Continuous improvement, adjustments, and dedication from all levels of a company are required to achieve zero defects in quality management. Organizations should better understand their consumers’ needs in order to build procedures that result in higher-quality goods or services.
It’s also critical to have mechanisms in place that can detect problems before they become severe enough to result in consumer damage or complaints. Organizations will be able to avoid costly mistakes that could harm their reputation and revenue in the long run.
Watch this video: WHAT IS BUSINESS IMPACT OF IMPROVING QUALITY
0
12844