Six Sigma DMADV and DMAIC – How Similar and Different are they?
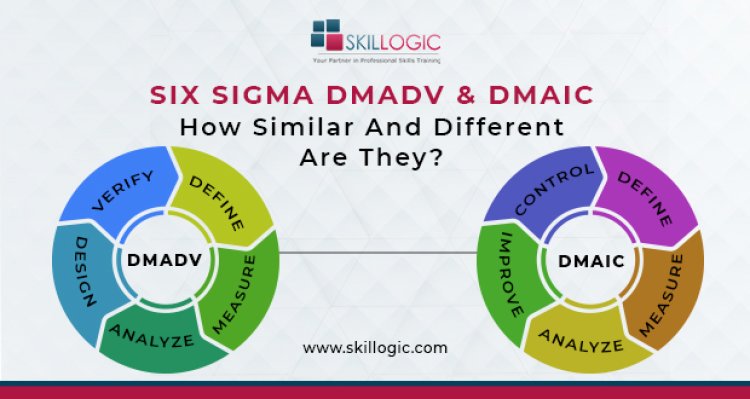
Six Sigma is a disciplined, data-driven process for terminating defects in any process within businesses or organizations. It was first launched by Motorola in 1985 as statistical modeling of manufacturing processes.
During the decision-making process, especially in the automotive sector, the success of an organization lies in its ability to respond quickly to the needs of its customers. This customer needs should be accompanied by low production costs and minimum lead time to introduce a product to the market, and deliver better performance than existing competitors in the market.
Six Sigma is a potent weapon that helps reduce costs. Preventing defects and enhancing products and processes results in higher profit and greater market share. This is achieved through two of the six Six Sigma methods: DMAIC and DMADV
DMAIC and DMADV are the two popular Six Sigma methods being put to use today. Businesses count on them to produce high-quality products and services with minimal defects while meeting customer expectations. While both are designed to help businesses run smoothly and efficiently, they are certainly not flexible and adapted to a variety of processes.
DMAIC:
DMAIC is a well-known and widely used LSS project method. DMAIC centers around enhancing the existing processes of businesses. It is a five-step strategy used to upgrade various organizational processes, whether it be software development, production, or post-production. DMAIC recognizes and tackles inefficiencies, which boost its outcomes and make these advancements more manageable.
The acronym DMAIC stands for the five phases as in Define, Measure, Analyse, Improve, and Control. The word is DMAIC pronounced “de-may-ick,” and is a tool for improvising an existing process.
D – as in Define; here businesses are able to define or identify the problem or inconsistencies in their processes. Also, they define and set out their processes, what is to be improved, who are their customers.
In this first step, the terms of the project and the internal and external customer service are explained. This section focuses on selecting projects that have the greatest impact and understanding which metrics will determine the success of a project. Who are the customers and what are their needs in terms of services and products? What do they expect? The parameters of the project are defined, including starting and stopping points, the flow of the process is indicated.
M – as in Measure; here businesses collect data from the process to establish a baseline for the improvements. Here businesses figure what parameters need to be quantified, devise the best way to measure them, gather the necessary data, and implement the measurements by experiment.
A – as in Analyze; here businesses analyze their data in order to find the root cause of defects. Pinpoint gaps between actual and goal performance, locate causes of those gaps, discover how process inputs affect outputs, and rank improvement opportunities.
I – as in Improve; here businesses develop, test, and implement solutions to improve the process. Construct potential solutions, discover solutions that are easiest to implement, check hypothetical solutions, and carry out actual improvements.
C – as in Control; here businesses implement process controls to sustain the improvements. Initiate a detailed solution monitoring plan, remark implemented improvements for success, upgrade plan records on a regular basis, and preserve a workable employee training routine
DMADV:
DMADV is a six sigma methodology that draws new processes, products, services in contrast to enhancing a previously existing one and makes it worthy for the first time. DMADV is convenient in bringing about new tactics and techniques because of its basis in data, fast detection of success, and rigorous analysis.
DMADV centers around the process of designing and developing a new product, service, or process. The different phases in DMADV are:
Design; In the first phase, goals are discovered and formulated according to the purpose of the project. Businesses come up with logical and noticeable goals that are set that are inevitable to both the organization and its stakeholders. After setting the goal, a clear scope must be defined for the project and a striking strategy must be in coordination with each of the project goals that will realize the expectation of the organization and the customers.
Measure; The second step in DMADV is Measure. In this step, the factors that are crucial to quality management should be measured. It’s necessary to describe the requirements of the metrics. The metrics should be measured in a way to deliver useful answers. It must acquire quality, risk, process capability, and product capability among others.
Analyze; The analysis phases include instigating design alternatives, identifying the optimal combination of requirements to attain a value within the given constraint
Develop; The fourth stage of DMADV calls for an eminent and intricate design. Each component of the design is given priority after which a high-level design is developed. After the creation of this high-level, a more elaborate design will be formulated as a prototype. Here, any errors which may happen can be discovered and the new process design can be remodeled to avoid any possible errors.
Verify; In the final phase of DMADV, it is time for the team to confirm that the design is sufficient. Is it relevant in the real world? This stage necessitates pilot studies and production-scale studies. The major aim is to make sure that the final product is of the best quality. The Verify step of DMADV consists of plan execution that specifies how the new process will evolve into routine operation.
Differences: DMAIC and DMADV
- DMAIC is about minimizing the divergence in existing processes while DMADV is about constructing process “for the first time:”
- DMAIC deals with correction while DMADV deals with blocking
- DMAIC uses mathematical tools while DMADV uses quality tools as KANO models
- DMAIC centers around critical QTC parameters while DMADV centers around all the parameters
- DMAIC is usually a shorter project than a long-term DMADV.
- Where DMAIC deals with processes as they are, DMADV deals with the design process.
- DMAIC implements control to maintain benefits, DMADV introduces measures to ensure that the completed project is operational and valid.
While most of the examples provided come from the production area, Six Sigma can be used to better any process in any environment. It is not limited to improving existing systems but can be used to design completely new processes as we have seen in this article. DMADV is an effective way to employ Six Sigma to think creatively and to reinvigorate processes that are so broken that they cannot be repaired in the normal way of DMAIC.
When DMAIC works well, DMADV works. When DMAIC introduces specific problem-solving strategies, DMADV is part of the process of developing a specific problem-solving approach.
Similarities: DMAIC and DMADV
Both methods:
- Use the structure to reduce error and solve problems.
- Focus on customers.
- Use collaboration to solve problems.
- Gather and inspect data to support decisions
- Share many similar tools, such as Failure Mode & Effects Analysis (FMEA), Design of Experiments (DOE), and reflection.
Conclusion:
As Six Sigma prevails to develop and care for the goals and objectives of the 21st-century business, professionals who speak the knowledge of these methods can find many suitable opportunities in a variety of industry sectors.
Learning Six Sigma can have a far-fetched influence on your future. Having a Six Sigma certification is equivalent to having promising abilities and skills to succeed in any organization. Get certified in Six Sigma from SKILLOGIC, we are accredited by ICFQ and TUV. Are you ready to stand out in the crowd? Apply now.
0
13643