Comparing Total Quality Management (TQM), Six Sigma, and Lean Methodologies
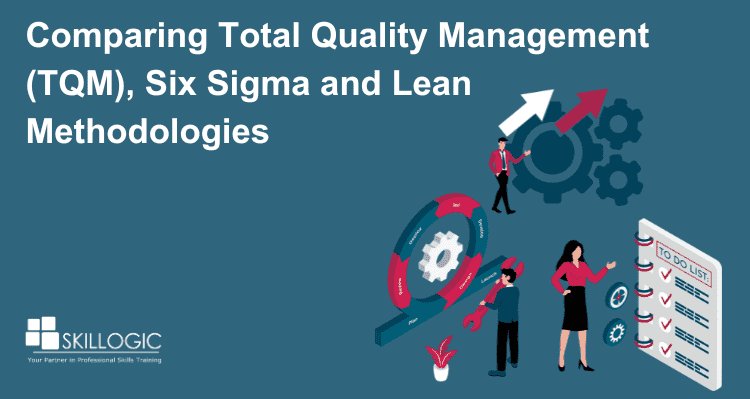
In today's business world, making things better and delivering top-notch products or services is key. This article dives into comparing three big methods for doing just that: Total Quality Management (TQM), Six Sigma, and Lean. Each method has its own way of making things run smoother and improving quality. We'll break down what each method is about, what tools they use, and how they help businesses. By looking closely at these methods, we'll help you figure out which one might work best for your business needs.
Understanding Total Quality Management (TQM):
Total Quality Management (TQM) stands as a comprehensive management philosophy aiming to enhance product and service quality by involving every member of an organization in continuous improvement efforts. Originating in the mid-20th century and flourishing in the 1980s and 1990s, particularly in Japan and the United States, TQM reflects a response to escalating demands for superior product standards.
Its core principles embody:
- Customer Focus: To guarantee client happiness and loyalty, it is important to comprehend and satisfy their requirements and expectations.
- Continuous Improvement: The relentless pursuit of better processes, products, and services through ongoing refinement and innovation.
- Employee Involvement: Recognizing that the commitment and contributions of all employees are vital to achieving and sustaining quality excellence.
As per Verified Market Research, the global Quality Management Software (QMS) market was valued at USD 7.56 billion in 2019 and is forecasted to reach USD 16.04 billion by 2027, growing at a CAGR of 9.9% from 2020 to 2027. This significant growth reflects the increasing adoption of QMS solutions across industries to improve product quality, streamline processes, and ensure regulatory compliance. Factors such as rising quality standards, digitalization, and the need for efficient risk management are driving the demand for QMS software, indicating continued expansion in the market.
Successful implementations of TQM can be witnessed in renowned companies like Toyota, Ford, and Motorola. These organizations have reaped the benefits of TQM, including heightened product quality, increased customer satisfaction, and enhanced overall business performance.
Read these articles:
Understanding Six Sigma:
Six Sigma is a methodology widely adopted by organizations to systematically improve processes and reduce defects, leading to enhanced efficiency and customer satisfaction. Originating from Motorola in the 1980s and popularized by companies like General Electric in the 1990s, Six Sigma emphasizes rigorous data analysis and statistical methods to identify and eliminate variations causing defects or errors. Obtaining a Lean Six Sigma Black Belt certification demonstrates a high level of expertise in these techniques.
Fundamentally, Six Sigma adheres to the DMAIC framework:
- Define: Clearly outline the problem, project goals, and customer requirements.
- Measure: Quantify existing process performance using relevant metrics and data collection techniques.
- Analyze: Investigate root causes of defects through statistical analysis and identify areas for improvement.
- Improve: Put solutions in place to deal with problems found and enhance process efficiency.
- Control: Establish measures to sustain improvements and prevent regression.
Key features of Six Sigma include a relentless focus on defect reduction, reliance on data-driven decision-making, and a commitment to continuous process improvement.
Several organizations have achieved remarkable success through Six Sigma implementation. For instance, General Electric famously saved billions of dollars by reducing defects and improving operational efficiency, while companies like Motorola and Honeywell have also experienced significant performance enhancements attributed to Six Sigma methodologies.
Understanding Lean Six Sigma:
Lean methodology, stemming from the renowned Toyota Production System (TPS), stands as a systematic approach to streamline processes, eliminate waste, and optimize efficiency across various industries. Originating in Japan and gaining prominence in the manufacturing sector during the post-World War II era, Lean principles have since transcended organizational boundaries to revolutionize operations in service and healthcare industries worldwide.
Central to Lean methodology are principles derived from TPS, emphasizing:
- Waste Reduction: Identifying and eliminating activities that do not add value to the end product or service, such as overproduction, waiting times, unnecessary transportation, excess inventory, overprocessing, defects, and underutilized talent.
- Value Stream Mapping: Visualizing and analyzing the flow of materials and information required to deliver a product or service to customers, enabling organizations to identify bottlenecks, inefficiencies, and opportunities for improvement.
- Continuous Flow: Designing processes to enable a smooth and uninterrupted flow of work, minimizing delays and improving throughput.
Examples of Lean implementation abound across diverse sectors. In manufacturing, companies like Toyota have achieved remarkable success by embracing Lean principles to streamline production processes and enhance quality. In the service industry, organizations like Southwest Airlines have revolutionized their operations through Lean methodologies, while healthcare providers such as Virginia Mason Medical Center have improved patient care and efficiency through Lean initiatives. Obtaining a Lean Six Sigma Green Belt certification can further enhance these efforts by providing individuals with the skills to implement Lean strategies effectively.
Refer to these articles:
- Six Sigma Certification Training Course Cost in India
- Why Six Sigma Certification in India?
- PMP Certification Training Course Cost in India
Comparative Analysis of Quality Management Methodologies: TQM, Six Sigma, and Lean
In comparing Total Quality Management (TQM), Six Sigma, and Lean methodologies, distinct differences emerge alongside areas of overlap and complementary features.
Key Differences:
Approach:
- TQM: Takes a holistic approach, involving all members of the organization in continuous improvement efforts, emphasizing customer satisfaction and organizational culture.
- Six Sigma: Focuses on reducing defects and variations within processes through statistical analysis and data-driven decision-making, aiming for near-perfection.
- Lean: Centers on waste reduction, optimizing process flow, and enhancing efficiency, often through the elimination of non-value-added activities.
Tools and Techniques:
- TQM: Utilizes tools such as quality circles, Pareto analysis, and cause-and-effect diagrams to identify and address quality issues.
- Six Sigma: Relies heavily on statistical tools like DMAIC (Define, Measure, Analyze, Improve, Control), hypothesis testing, and regression analysis to drive process improvements.
- Lean: Leverages techniques such as value stream mapping, 5S, Kanban, and Just-in-Time (JIT) production to streamline operations and eliminate waste.
Philosophy:
- TQM: Emphasizes continuous improvement, employee involvement, and customer focus as fundamental to organizational success.
- Six Sigma: Strives for process excellence and defect reduction, driven by measurable, data-backed goals and a relentless pursuit of improvement.
- Lean: Promotes a culture of continuous flow, waste elimination, and value creation, aiming to maximize efficiency and deliver products or services with minimal resources.
Areas of Overlap and Complementarity:
- Continuous Improvement: TQM, Six Sigma, and Lean share a commitment to ongoing improvement, fostering adaptability and responsiveness.
- Customer Focus: Prioritizing customer satisfaction is central to all three methodologies, strengthening relationships and driving growth.
- Employee Engagement: Each methodology values employee involvement, empowering teams to drive quality initiatives.
- Data-Driven Decisions: Emphasizing data, organizations make informed choices, mitigating risks and identifying opportunities.
- Holistic Quality Approach: Recognizing quality's multifaceted nature, organizations integrate strategies for comprehensive improvement.
Strengths and Weaknesses:
TQM:
- Strengths: Comprehensive approach, emphasis on employee involvement and customer satisfaction foster a culture of quality throughout the organization.
- Weaknesses: Lack of specific tools and methodologies for quantitative analysis may result in slower decision-making and implementation.
Six Sigma:
- Strengths: Rigorous statistical analysis and structured methodologies lead to significant defect reduction and process optimization, resulting in tangible financial benefits.
- Weaknesses: Over-reliance on data analysis may stifle creativity, and the resource-intensive nature of Six Sigma projects may pose challenges for some organizations.
Lean:
- Strengths: Focus on waste reduction and process efficiency leads to streamlined operations, increased productivity, and improved customer satisfaction.
- Weaknesses: Lean initiatives may overlook quality aspects in pursuit of efficiency gains, and resistance to change from employees accustomed to traditional workflows can hinder implementation.
Considerations for Selection:
When choosing a methodology, organizations should consider:
- Strategic Objectives: Select the methodology that best aligns with the organization's goals and priorities.
- Organizational Culture: Ensure compatibility with the existing culture to facilitate smooth implementation and acceptance among employees.
- Resource Availability: Assess the organization's resources, including budget, expertise, and time, to determine feasibility and sustainability of the chosen methodology.
By carefully evaluating these factors, organizations can select the most appropriate methodology to drive continuous improvement and achieve their desired business outcomes.
Applications of Total Quality Management (TQM), Six Sigma, and Lean Methodologies
Toyota:
Lean Methodology: Toyota's implementation of Lean principles within its production system revolutionized the automotive industry. By emphasizing waste reduction and continuous improvement, Toyota achieved remarkable efficiency gains and quality improvements.
General Electric (GE):
Six Sigma: GE's adoption of Six Sigma methodologies led to significant cost savings and quality improvements across its diverse business units. Through rigorous data analysis and process optimization, GE achieved measurable reductions in defects and enhanced customer satisfaction.
Motorola:
Six Sigma: Motorola pioneered Six Sigma methodologies in the 1980s, resulting in substantial quality improvements and cost savings. By focusing on defect reduction and process optimization, Motorola set new standards for quality excellence in the telecommunications industry.
Ford:
Total Quality Management (TQM): Ford's implementation of TQM principles in the 1980s helped the company regain competitiveness in the automotive market. By emphasizing customer focus and continuous improvement, Ford achieved significant quality improvements and operational efficiencies.
Virginia Mason Medical Center:
Lean Methodology: Virginia Mason Medical Center successfully applied Lean principles to healthcare delivery, resulting in improved patient outcomes and operational efficiency. By eliminating waste and optimizing processes, Virginia Mason reduced wait times, enhanced patient satisfaction, and improved clinical outcomes.
Challenges in Implementing Total Quality Management (TQM), Six Sigma, and Lean Methodologies
Resistance to Change:
Organizations often face resistance from employees accustomed to traditional ways of working. Successful implementation requires effective change management strategies and strong leadership support to overcome resistance and foster a culture of continuous improvement.
Data Quality and Availability:
Effective implementation of TQM, Six Sigma, and Lean methodologies relies on accurate and accessible data. Organizations may encounter challenges related to data quality, availability, and integration. Investing in data infrastructure and analytics capabilities is essential to support informed decision-making and drive sustainable improvements.
Siloed Thinking:
Siloed organizational structures and departmental boundaries can hinder collaboration and alignment. Successful implementation requires breaking down silos and fostering cross-functional collaboration to address end-to-end processes and deliver holistic solutions.
Sustainability:
Sustaining improvement gains over the long term requires ongoing commitment and vigilance. Organizations must embed quality management principles into their culture, processes, and systems to ensure continuous improvement becomes ingrained in the organizational DNA.
Balancing Trade-Offs:
Implementing TQM, Six Sigma, or Lean methodologies often involves trade-offs between competing priorities such as cost, quality, and speed. Organizations must carefully balance these trade-offs and align improvement efforts with strategic objectives to maximize value creation and long-term success.
Read the following articles:
- Six Sigma Certification Cost in Bangalore
- Lean Six Sigma Certification Cost in Chennai
- Lean Six Sigma Certification Cost in Pune
Future Trends and Emerging Practices in Quality Management
As organizations strive for continuous improvement and innovation, several trends are shaping the future landscape of quality management:
- Digital Transformation: The integration of digital technologies, such as Artificial Intelligence (AI), Internet of Things (IoT), and big data analytics, is revolutionizing quality management. AI-powered predictive analytics can anticipate quality issues before they occur, IoT devices enable real-time monitoring of production processes, and big data analytics provide actionable insights for decision-making.
- Industry 4.0 and Smart Manufacturing: Industry 4.0 principles, including automation, connectivity, and data exchange, are driving the adoption of smart manufacturing practices. By leveraging interconnected systems and advanced technologies, organizations can optimize production processes, minimize defects, and enhance product quality.
- Customer-Centric Quality: Customer expectations are evolving, necessitating a shift towards customer-centric quality management. Organizations are increasingly focusing on understanding customer needs and preferences, soliciting feedback, and delivering personalized products and services to enhance customer satisfaction and loyalty.
- Agile and Lean Principles: Agile methodologies, originally developed for software development, are being applied to quality management to enable rapid adaptation to changing market dynamics and customer requirements. Similarly, Lean principles continue to be embraced for their focus on waste reduction, continuous improvement, and value creation.
- Sustainability and Environmental Responsibility: With growing concerns about environmental sustainability, organizations are incorporating environmental management practices into their quality management systems. By minimizing waste, reducing energy consumption, and adopting eco-friendly production processes, organizations can achieve both quality and sustainability goals.
- Risk Management and Resilience: In an increasingly complex and uncertain business environment, risk management is becoming integral to quality management. Organizations are proactively identifying and mitigating risks that could impact product quality, supply chain continuity, and overall business performance, thereby enhancing resilience and agility.
- Collaborative Supply Chains: Quality control is now applied throughout the whole supply chain, spanning organizational boundaries. Collaborative quality initiatives involve close collaboration with suppliers and partners to ensure consistency, transparency, and compliance throughout the value chain.
Selecting the right quality management methodology is vital for organizational excellence. Each approach offers unique benefits, so careful assessment is crucial. Further learning through resources like books and courses can deepen understanding. Implementing these methodologies fosters continuous improvement and success. For Six Sigma Training, SKILLOGIC offers accredited courses, ensuring quality education. As a leading provider, SKILLOGIC institute equips professionals with essential skills and certifications for effective quality management.
0
1164